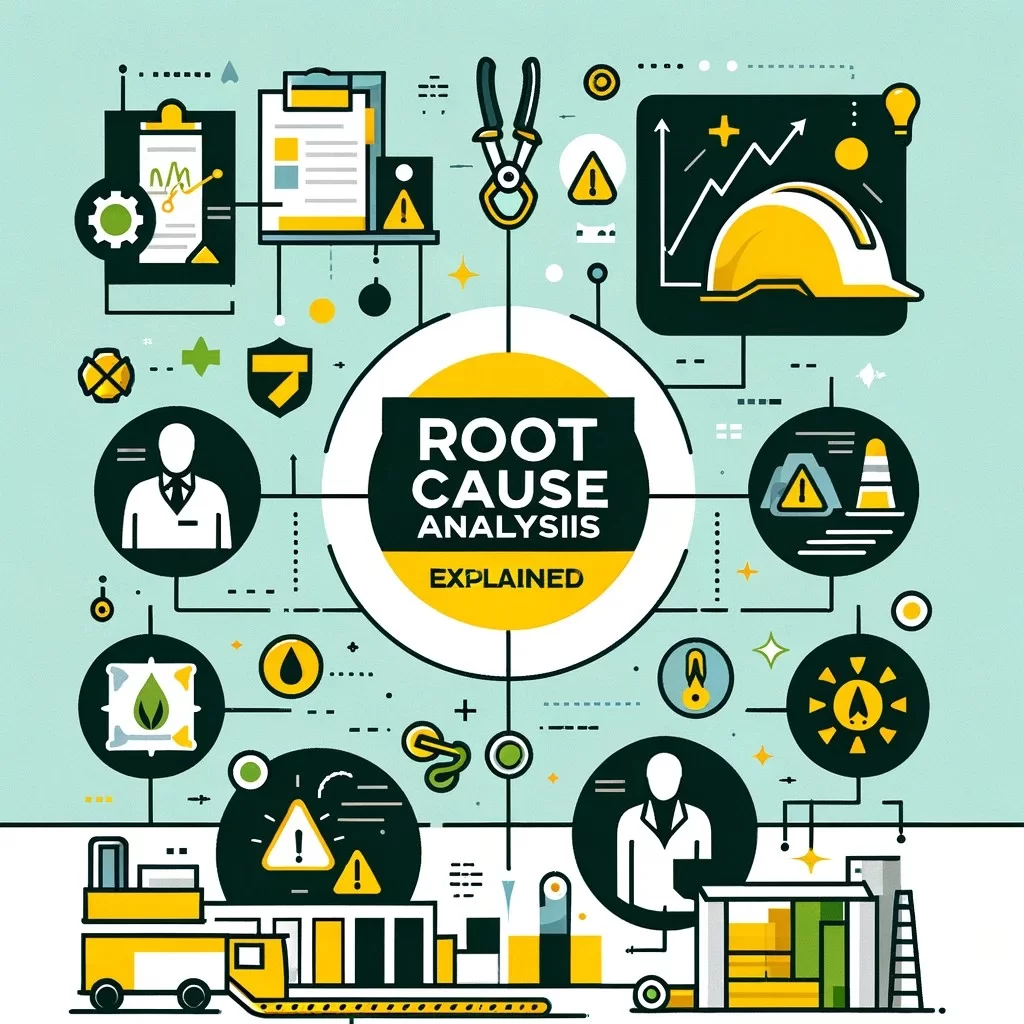
Kaza Kök Neden Analizinin Önemi
Kaza kök neden analizi (KKNA), iş kazalarının ya da olaylarının yüzeyindeki belirtileri değil, derinlemesine nedenlerini araştırarak, kazaların tekrarını önlemeyi amaçlayan bir tekniktir. Bu analiz, bir kaza veya olay sonrasında, kazanın sadece ne olduğunu değil, nasıl ve neden meydana geldiğini anlamaya odaklanır. Kaza kök neden analizi, kazaların arkasındaki temel sebepleri ortaya koyarak daha kalıcı çözümler geliştirilmesine yardımcı olur. Böylece, benzer olayların gelecekte yaşanması engellenebilir. Bu süreç, iş sağlığı ve güvenliği açısından büyük bir öneme sahiptir.
Kaza Kök Neden Analizinin Temel Amaçları
Kaza kök neden analizinin en önemli amacı, kazaların nedenlerini yüzeysel bir şekilde değil, derinlemesine incelemektir. Bu analiz, kaza sonrasındaki tüm etmenleri göz önünde bulundurarak kazaların arkasındaki gerçek nedenleri anlamayı hedefler. Yalnızca kazanın sonucuna değil, olayın oluşmasına neden olan faktörlere de odaklanır. Bu şekilde kazaların önlenmesi ve gelecekteki benzer kazaların engellenmesi sağlanabilir. Ayrıca, kaza kök neden analizi, güvenlik kültürünün güçlendirilmesine yardımcı olur. İleriye dönük olarak daha güvenli bir çalışma ortamı sağlamak için kazanın temel nedenlerine yönelik çözümler önerilir.
Kaza Kök Neden Analizinde Kullanılan Yöntemler
Kaza kök neden analizi (KKNA), kazaların altında yatan temel sebepleri bulmak için çeşitli yöntemler ve araçlar kullanır. Bu yöntemler, kazaların yüzeysel sebeplerini değil, daha derinlemesine nedenlerini anlamaya odaklanır. Her bir yöntem, farklı analiz perspektifleri sunar ve kazaların oluşumunun karmaşık dinamiklerini ortaya koyar. İşte kaza kök neden analizinde yaygın olarak kullanılan başlıca yöntemler:
1. 5 Neden Tekniği (5 Whys)
"5 Neden" tekniği, kök neden analizinin en temel ve yaygın kullanılan yöntemlerinden biridir. Bu yöntem, bir olayın nedenlerini bulmak için "Neden?" sorusunun tekrarlanarak sorulmasıyla uygulanır. Genellikle, bir kaza veya olayın nedenini belirlemek için 5 kez sorulan "neden" sorusu, derinlemesine bir analiz sürecini başlatır.
Uygulama: Bir olayla ilgili ilk neden belirlendikten sonra, bu nedenin arkasındaki bir sonraki sebepler de aynı şekilde "neden?" sorusu ile araştırılır. Bu işlem, kazanın temel nedenine ulaşana kadar devam eder. Genellikle, 5 kez bu soruyu sormak, temel nedenlere ulaşmak için yeterlidir. Ancak, bazen daha fazla ya da daha az soru sorulabilir. Bu analiz, basit ve hızlı bir yöntemdir ancak karmaşık olaylar için derinlikli bir inceleme gerektirebilir.
Örnek: Bir işyerinde çalışan bir kişi yere düşüp yaralanmıştır. Bu durumu "5 Neden" tekniğiyle analiz edersek:
-
- Neden: Çalışan yere düştü.
- Neden: Yere dökülen sıvıyı temizlememişti.
- Neden: Temizlik malzemeleri düzgün bir şekilde yerleştirilmemişti.
- Neden: Temizlik ekipmanları düzenli olarak kontrol edilmiyordu.
- Neden: Temizlik prosedürleri yeterince eğitimle aktarılmıyordu.
Bu durumda, 5. neden (eğitim eksikliği) aslında kazanın temel kök nedenidir.
2. Fishbone Diyagramı (Balık Kemiği Diyagramı)
Fishbone diyagramı, Japon kökenli bir analiz aracıdır ve özellikle karmaşık sorunları çözmede etkili bir yöntemdir. Bu diyagram, bir olayın nedenlerini görsel olarak sunar ve ana sebep kategorilerini belirler. Bu araç, genellikle "İnsan", "Makine", "Malzeme", "Yöntem" ve "Çevre" gibi ana kategorilere dayanır. Bu kategori başlıkları altında, olayın oluşmasına katkıda bulunan tüm etmenler sıralanır.
Uygulama: Fishbone diyagramı, her bir kategori altındaki potansiyel nedenleri detaylı şekilde listelemeyi sağlar. Bu sayede, olayın sadece yüzeydeki etkilerini değil, arkasındaki çok sayıda faktörü daha iyi kavrayabiliriz. Görsel olarak, tüm nedenler bir balık kemiği gibi düzenlenir, bu da analiz sürecini daha anlaşılır hale getirir.
Örnek: Bir üretim hattındaki arızayı analiz etmek için kullanılan Fishbone diyagramı, aşağıdaki gibi kategorilerde incelenebilir:
- İnsan: Yetersiz eğitim, dikkatsizlik, deneyimsizlik
- Makine: Arızalı makineler, bakım eksiklikleri
- Malzeme: Düşük kaliteli malzeme, yanlış malzeme kullanımı
- Yöntem: Hatalı üretim prosedürleri, verimsiz iş akışı
- Çevre: Aydınlatma eksiklikleri, gürültü kirliliği
3. FMEA (Hata Türü ve Etkileri Analizi)
FMEA, bir sistem, süreç veya üründeki potansiyel hata türlerini belirleyip bu hataların olası etkilerini değerlendiren bir analiz yöntemidir. FMEA, genellikle ürün geliştirme ve üretim süreçlerinde kullanılır, ancak iş kazaları ve güvenlik ihlalleri gibi konularda da uygulanabilir.
Uygulama: FMEA, her bir hata türü için olasılık, şiddet ve tespitin zorluğu gibi faktörleri değerlendirir. Bu üç faktör, her hata için bir Risk Öncelik Sayısı (RPN) hesaplamak için kullanılır. Yüksek RPN değeri, o hatanın daha fazla dikkat gerektirdiğini gösterir.
Örnek: Bir güvenlik prosedürünü FMEA ile değerlendirirken, şu adımlar takip edilebilir:
- Hata Türü: Çalışanların güvenlik kasklarını takmaması
- Etkiler: Çalışanlar kafa travması geçirebilir.
- Olasılık: %10 olasılık
- Şiddet: Yüksek (ölüm riski)
- Tespit Zorluğu: Orta (görsel kontrolle tespit edilebilir)
RPN hesaplandıktan sonra, bu hata için çözüm önerileri geliştirilebilir.
4. FTA (Kök Neden Analizi - Fault Tree Analysis)
Fault Tree Analysis (FTA), bir olayın olma olasılığını ve o olayın gerçekleşmesine neden olan etmenleri inceleyen daha karmaşık bir yöntemdir. Bu yöntem, belirli bir kazanın gerçekleşmesinin olasılığını daha detaylı bir şekilde değerlendirir ve sistematik bir şekilde kök nedenleri araştırır. Bu analizde, olay bir "kök neden ağacı" şeklinde yapılandırılır ve her bir nedenin potansiyel sonuçları gösterilir.
Uygulama: FTA, özellikle büyük ve karmaşık sistemlerde kullanılır. Sistemdeki bir hatanın ana nedenleri belirlenerek, bu nedenlerin her birinin olasılığı ve etkisi hesaplanır. Daha sonra, bu nedenlerin ortadan kaldırılmasına yönelik stratejiler geliştirilir.
Örnek: Bir endüstriyel makinedeki arıza FTA ile incelenirken, şu adımlar izlenebilir:
- Başlangıç Olayı: Makine çalışmıyor.
- Olası Nedenler: Elektrik kesintisi, donanım arızası, yazılım hatası.
- Alt Nedenler: Elektrik kesintisi için güç kaynağı arızası, donanım arızası için aşırı ısınma, yazılım hatası için güncelleme eksikliği.
5. HAZOP (Tehlike ve Operasyonel Durum Değerlendirmesi)
HAZOP, özellikle kimya, petrol ve doğal gaz endüstrilerinde kullanılan bir risk analiz yöntemidir. Bu yöntem, belirli bir süreç veya sistemin işleyişinde tehlikeli olabilecek her durumu ve durumun nasıl kontrol edileceğini belirlemeyi amaçlar.
Uygulama: HAZOP, bir ekip tarafından yürütülür ve süreç adımlarındaki her türlü sapma analiz edilir. Sapmalar, genellikle "ne olursa" sorusu ile değerlendirilir. Örneğin, "Ne olur eğer sistemde basınç yükselirse?" sorusu, olası tehlikeleri ve bunlara karşı alınabilecek önlemleri anlamak için kullanılır.
Örnek: Bir fabrikada, sıcak suyun taşınmasındaki tehlikeleri değerlendiren bir HAZOP analizi şu soruları içerebilir:
- Ne olur eğer boru hattı tıkanırsa?
- Ne olur eğer suyun sıcaklığı beklenenden daha yüksek olursa?
- Ne olur eğer basınç düşerse?
Bu yöntem, belirli süreçlerdeki tüm potansiyel tehlikeleri ve sapmaları gözler önüne serer.
Kaza kök neden analizi için kullanılan bu yöntemler, her bir kazanın ya da olayın altında yatan karmaşık etmenleri anlamamıza yardımcı olur. Farklı yöntemler ve araçlar, kazaların kök nedenlerine ulaşmada farklı bakış açıları sunar. Kazaların etkili bir şekilde önlenmesi ve güvenli çalışma ortamları oluşturulması için bu analizlerin doğru ve kapsamlı bir şekilde uygulanması gerekmektedir.
İnsan Faktörlerinin ve Organizasyonel Zorlukların Rolü
Kaza kök neden analizi, yalnızca teknik sorunları değil, aynı zamanda insan faktörlerini ve organizasyonel zorlukları da göz önünde bulundurur. İnsan hatası, kazaların başlıca sebeplerinden biri olabilir. Ancak bu faktör, sadece bireylerin dikkat eksikliği veya yanlış kararlar almasıyla açıklanamaz. İnsan hatası, genellikle organizasyonel eksiklikler, yetersiz eğitim, iletişim sorunları ve yetersiz denetim gibi faktörlerle de ilişkilidir. Bu nedenle, etkili bir kök neden analizi, hem bireysel hataları hem de sistemsel sorunları değerlendirir.
Kaza Kök Neden Analizinin İş Güvenliği Üzerindeki Katkıları
Kaza kök neden analizi, iş güvenliğini artırmak için kritik bir araçtır. Bu analiz, kazaların kök sebeplerini belirleyerek, alınması gereken önlemleri tespit eder. Aynı zamanda, kazaların sebepleri hakkında kapsamlı bir bilgi sağlayarak, benzer olayların tekrarlanmaması için organizasyonların stratejiler geliştirmesini sağlar. Bu süreç, organizasyonel değişiklikler ve geliştirmeler gerektirebilir. Örneğin, bir güvenlik protokolündeki eksiklikler, çalışan eğitiminde yetersizlikler ya da ekipman arızaları tespit edilebilir. Kök neden analizi, bu sorunları çözerek güvenlik önlemlerinin etkinliğini artırır.
Çalışanların Katılımı ve Güvenlik Kültürü
Kaza kök neden analizi, yalnızca yöneticilerin değil, tüm çalışanların katılımını gerektirir. Çalışanların olaylara dair geri bildirimleri, kazaların kök nedenlerini anlamada önemli bir rol oynar. Bu süreç, çalışanların güvenlik kültürüne olan bağlılıklarını artırır. Ayrıca, çalışanlar kazaların sebeplerine dair daha fazla bilgi edinir ve güvenlik konusunda daha bilinçli hale gelirler. Bu, daha güvenli bir çalışma ortamının oluşturulmasında büyük önem taşır.
Sonuç olarak, kaza kök neden analizi, iş yerlerinde güvenliği artırmak ve kazaların önüne geçmek için oldukça önemli bir tekniktir. Yalnızca kazaların yüzeyel nedenlerine odaklanmak yerine, derinlemesine bir inceleme yaparak, kazaların arkasındaki temel sebepler ortaya konur. Bu analiz, daha güvenli bir çalışma ortamı sağlamanın yanı sıra, organizasyonel değişimlere de yol açabilir. Kök neden analizi, sadece kazaların engellenmesine yardımcı olmakla kalmaz, aynı zamanda güvenlik kültürünün güçlenmesine de katkıda bulunur.